Just how to Select the Correct Products for Rotomolding
Rotational molding, commonly referred to as rotomolding, is really a flexible production process applied to create durable and complex plastic products. One of many important facets influencing the success of a rotomolding challenge is the option of material. The selection method may considerably impact the product quality, performance, and durability of the final product. Here is a brief manual to assist you pick the best components for your following Plastics Rotomolding project.
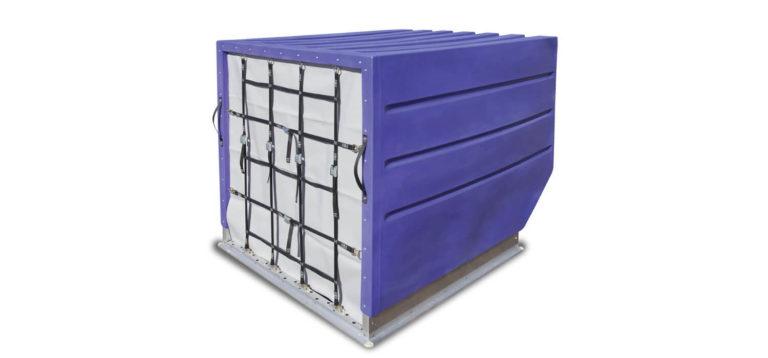
Understand the Application Demands
The first faltering step in material collection is to understand the particular application of the product you are manufacturing. Consider factors such as the atmosphere in which the item will be used, if it will be exposed to intense conditions, UV rays, or severe compounds, and the mandatory durability. As an example, outdoor applications often necessitate resources with UV weight to ensure prolonged operation and small degradation.
Key Material Qualities to Evaluate
When choosing products for rotomolding, prioritize the next features depending on your own project goals:
• Longevity: Opt for products that will experience technical stress without breaking or failing. Services and products utilized in industrial or heavy-duty purposes benefit from high-impact resistance.
• Mobility: For products that need to keep up their integrity under some pressure or twisting, resources with good flexibility, such as for instance polyethylene (PE), are often suitable.
• Chemical Opposition: If the product will come in to experience of substances, fuels, and other harsh brokers, guarantee the product won't weaken or react adversely.
• Heat Opposition: Products and services exposed to high-temperature problems need resources capable of maintaining their architectural integrity without warping or melting.
• Environmental Affect: Several industries are turning toward sustainable resources for manufacturing. If eco-friendliness is really a priority, consider recyclable or biodegradable materials.
Popular Materials for Rotomolding
Rotomolding is compatible with a variety of products, each giving unique houses:
• Polyethylene (PE): Widely used and functional, PE presents longevity, impact weight, and compound stability at a reasonable cost. High-Density Polyethylene (HDPE) or Linear Low-Density Polyethylene (LLDPE) are normal possibilities according to particular needs.
• Polypropylene (PP): Known for their outstanding chemical resistance and energy, PP is a practical selection for professional and automotive components.
• Nylon: Giving high energy, use opposition, and heat patience, nylon is ideal for heavy-duty applications.
• Crosslinked Polyethylene (XLPE): This substance provides exceptional durability and is often chosen for applications requesting remarkable impact strength.
Product Screening and Prototyping
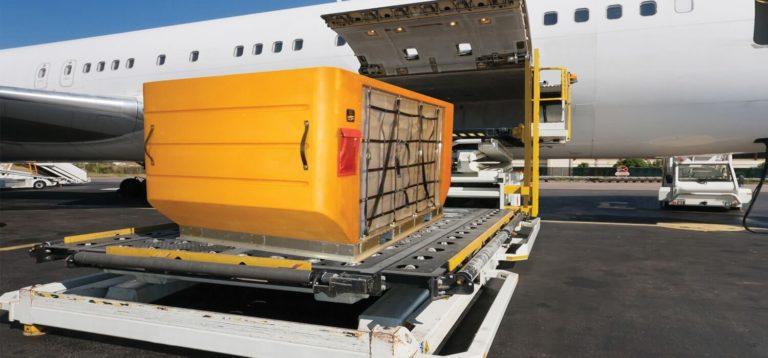
To ensure your picked substance meets all necessary requirements, perform complete screening and prototyping. Examine your material in real-world conditions to detect any weaknesses or inconsistencies before getting into complete production.
Ultimate Feelings
The proper material selection in rotomolding will make or separate your product's success. Handling facets such as for example toughness, flexibility, and environmental sustainability assures optimal performance and customer satisfaction. Taking the time to gauge application-specific needs and product attributes provides long-lasting solutions and services and products that be noticeable in their respective markets.